Post Title 4
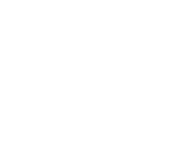
INDUSTRY
Process Manufacturing
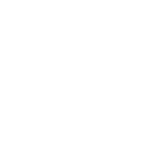
REGION
Canada
Process Manufacturing
Canada
The client stands as the forefront leader in geosynthetic material manufacturing and is dedicated to enhancing civil and environmental infrastructure worldwide.Established in Varennes, Quebec, the client has solidified its global presence through 32 legal entities across 4 continents strategically positioned across Canada, the USA, Germany, Malaysia, Thailand, Egypt, China, and Australia. This extensive network encompasses 10+ manufacturing units operating round-the-clock across various time zones to ensure continuous production and a robust logistical framework with 19 physical warehouses strategically located to serve its diverse clientele worldwide in multiple time zones. Therefore, the major challenge was standardizing business processes consistently across all countries.
Despite varying regulations across different countries, the goal was to project a unified brand identity. Whether it is company reports or other critical details, the presentation should reflect a single, standardized company. To address these challenges, The client launched the “One organization, One Data, and One Reporting” initiative. To support this initiative, The client was looking to develop comprehensive reports that provide a holistic view of the client’s global operations. They also required consistent reporting standards across all legal entities. Whether it’s financial data, performance metrics, or operational insights, common reporting ensures uniformity and accuracy.
The client faced several challenges with their previous systems, including Azure Data Factory ETL and BYOD. They needed full data pushes for every entity, resulting in long refresh times for Power BI reports, creating entities for individual tables, and managing schedules for batch jobs and report refreshments.
Despite previous engagements with Managed Service Providers (MSPs), The client found their existing solutions inadequate in addressing their unique requirements and expected results, necessitating a more robust and tailored approach to digital transformation.
The professionals at DynaTech provided top-notch consulting services to help the client choose the best solution for their enterprise. Our professionals recommended our robust Finance Optimization Solution to streamline their entire workflow and get everything on a single unified platform. We offered them a perfect blend of D365 F&O implementation, Power Automate, and Power BI Integration solutions that would help them resolve all their current and future challenges.
Production Planning and Scheduling Streamlined the order creation with the drag-and-drop feature,...
Production The production module helped simplify data entry, including roll posting with automatic...
Quality Control The quality control module streamlined data entry with a single form for test...
Product Master It simplified specification management with detailed properties, enabling...
Production Planning and Scheduling Streamlined the order creation with the drag-and-drop feature,...
Production The production module helped simplify data entry, including roll posting with automatic...
Quality Control The quality control module streamlined data entry with a single form for test...
Product Master It simplified specification management with detailed properties, enabling...
DynaTech Systems integrated Power Automate to streamline the quality testing process. Traditionally, quality checks involved users collecting manual data to assess the thickness and density of rolls. Additionally, integration with the Instron machine facilitated automated testing, but the results still required manual entry into Dynamics 365 F&O.
To address this, we developed a Power Automate Flow named “Lab Quality Result Import”. This flow automated the transfer of test results from the Instron machine directly into Dynamics 365 F&O. When test results are collected, they pass seamlessly through the Power Automate Flow, eliminating the need for manual intervention. This ensures that critical data regarding testing frequency, thickness, over-thickness, density, etc., are accurately captured and stored in the system without delay or errors, empowering the users to focus on higher-value tasks
DynaTech offered Power BI Integration that helped in aggregating data from multiple sources into a single dashboard, providing comprehensive insights at a glance. Scheduled inventory report refreshments every 3 hours empowered both production teams and management with up-to-date information. With customizable filters and various chart options, the client could visualize data tailored to their specific needs. The "Analyse in Excel" feature further enhanced data analysis capabilities. Additionally, we are providing ongoing support, developing and modifying dashboards as requested, and ensuring seamless access to Power BI for all users.
Streamlined the order creation with the drag-and-drop feature, machine capacity planning helped...
The production module helped simplify data entry, including roll posting with automatic raw...
The quality control module streamlined data entry with a single form for test results...
It simplified specification management with detailed properties, enabling...
Streamlined the order creation with the drag-and-drop feature, machine capacity planning helped...
The production module helped simplify data entry, including roll posting with automatic raw...
The quality control module streamlined data entry with a single form for test results...
It simplified specification management with detailed properties, enabling...
Streamlined operations through a single integrated system, reducing errors and enhancing efficiency.
Enhanced visibility across global operations, enabling informed decision-making.
Improved strategic planning with real-time insights and global reporting capabilities.
Higher customer satisfaction through faster response times and accurate order processing.
Simplified management of diverse legal entities and operations, leading to better compliance.
Cost savings achieved through optimized procurement, production, and logistics processes.
Greater control over finances with comprehensive reporting and analytics capabilities.
Power Automate Integration automated quality testing processes, reducing manual effort and potential errors while ensuring swift and accurate data transfer.
Empowering Global Operations with Unified Processes. The client stands as the forefront leader in geosynthetic material...
Empowering Global Operations with Unified Processes. The client stands as the forefront leader in geosynthetic material...
INTRODUCTION: Your “how to” blog post should teach the reader how to do something by breaking it down into a series of...