DynaTech’s Finance Optimization Solution Enables a Geosynthetic Manufacturing Company Escalate its Operational Efficiency
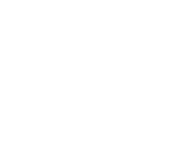
INDUSTRY
Process Manufacturing
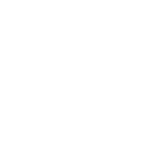
REGION
Canada
Process Manufacturing
Canada
The client stands as the forefront leader in geosynthetic material manufacturing and is dedicated to enhancing civil and environmental infrastructure worldwide. Established in Varennes, Quebec, the client has solidified its global presence through 32 legal entities across 4 continents strategically positioned across Canada, the USA, Germany, Malaysia, Thailand, Egypt, China, and Australia. This extensive network encompasses 10+ manufacturing units operating round-the-clock across various time zones to ensure continuous production and a robust logistical framework with 19 physical warehouses strategically located to serve its diverse clientele worldwide in multiple time zones. Therefore, the major challenge was standardizing business processes consistently across all countries.
Despite varying regulations across different countries, the goal was to project a unified brand identity. Whether it is company reports or other critical details, the presentation should reflect a single, standardized company. To address these challenges, The client launched the “One organization, One Data, and One Reporting” initiative. To support this initiative, The client was looking to develop comprehensive reports that provide a holistic view of the client’s global operations. They also required consistent reporting standards across all legal entities. Whether it’s financial data, performance metrics, or operational insights, common reporting ensures uniformity and accuracy.
The client was looking to modernize their legacy systems, including Azure Data Factory ETL and BYOD. They needed full data pushes for every entity, resulting in long refresh times for Power BI reports, creating entities for individual tables, and managing schedules for batch jobs and report refreshments.
To address these unique challenges and achieve the desired results, they sought a Managed Service Provider (MSP) that could offer a more robust and tailored approach to digital transformation.
The professionals at DynaTech provided top-notch consulting services to help the client choose the best solution for their enterprise. Our professionals recommended our robust Finance Optimization Solution to streamline their entire workflow and get everything on a single unified platform. We offered them a perfect blend of D365 F&SCM implementation, Power Automate, and Power BI Integration solutions that would help them achieve their desired results.
Streamlined the order creation with the drag-and-drop feature, machine capacity planning helped...
The production module helped simplify data entry, including roll posting with automatic raw...
The quality control module streamlined data entry with a single form for test results. It helped...
It simplified specification management with detailed properties, enabling product variations and...
It was integrated with BOM for accurate quotation calculations and control over future-dated raw...
It calculated costs based on roll quantity and distance traveled, ensuring accuracy. It maintained...
It was integrated with a mobile application for efficient loading and scanning. Two-click material...
It automatically generated serial/batch numbers during registration, ensuring traceability. Vendor...
It offered comprehensive functionality for transportation accrual, simplifying the settlement of...
DynaTech Systems integrated Power Automate to streamline the quality testing process. Traditionally, quality checks involved users collecting manual data to assess the thickness and density of rolls. Additionally, integration with the Instron machine facilitated automated testing, but the results still required manual entry into Dynamics 365 F&SCM.
To address this, we developed a Power Automate Flow named “Lab Quality Result Import”. This flow automated the transfer of test results from the Instron machine directly into Dynamics 365 F&SCM. When test results are collected, they pass seamlessly through the Power Automate Flow, eliminating the need for manual intervention. This ensures that critical data regarding testing frequency, thickness, over-thickness, density, etc., are accurately captured and stored in the system without delay or errors, empowering the users to focus on higher-value tasks
DynaTech offered Power BI implementation powered by Microsoft Fabric that helped in aggregating data from multiple sources into a single dashboard, providing comprehensive insights at a glance. Scheduled inventory report refreshments every 3 hours empowered both production teams and management with up-to-date information. With customizable filters and various chart options, the client could visualize data tailored to their specific needs. The "Analyse in Excel" feature further enhanced data analysis capabilities. Additionally, we are providing ongoing support, developing and modifying dashboards as requested, and ensuring seamless access to Power BI for all users.
Streamlined the order creation with the drag-and-drop feature, machine capacity planning helped prevent bottlenecks, and recipe change options ensured operational flexibility. Raw material shortage notifications enabled proactive planning, and color-coded status indicators offered clear visual progress tracking. Our system dynamically adjusts plans for any machine breakdowns, ensuring uninterrupted operations.
The production module helped simplify data entry, including roll posting with automatic raw material consumption based on order recipes and real-time inventory updates. Machine stop tracking enhances production planning, and machine-wise data entry screens streamline data capture. It also offers specification and label printing directly from the entry screen, enhancing workflow.
The quality control module streamlined data entry with a single form for test results. It helped distinguish between ISO and ASTM test methods for compliance, automated result calculations and displayed detailed roll information. Color coding highlights abnormal results for quick identification, while certifications are managed efficiently based on packing slips.
It simplified specification management with detailed properties, enabling product variations and defining quality testing with standard values. It offered flexibility with configuration for both imperial and metric units. The "TMA/Recipe" concept allowed controlled recipe selection based on process needs, with automatic BOM calculation for efficiency.
It was integrated with BOM for accurate quotation calculations and control over future-dated raw material prices. It enabled flexible pricing strategies with spreads based on product type and territory, and version control tracked cost fluctuations. Special pricing mechanisms catered to customized offerings, and automated workflows and email notifications streamlined approval processes. Users could define approval matrices and amend product dimensions to meet customer needs.
It calculated costs based on roll quantity and distance traveled, ensuring accuracy. It maintained separate data for domestic and international contracts, simplifying operations. Automatic price calculation based on transportation type streamlined estimation. Roll-to-transport mapping facilitated efficient cost allocation. Load simulation optimized delivery planning, while version control ensured accurate data.
It was integrated with a mobile application for efficient loading and scanning. Two-click material transfers between locations via mobile devices streamlined warehouse processes. Mobile reservation capabilities streamlined inventory management, and skid-building functionality optimizes packaging. Inter-warehouse transfers and multi-barcode scanning ensure seamless inventory movement and accurate tracking. Customizable production label management met diverse labeling needs effectively.
It automatically generated serial/batch numbers during registration, ensuring traceability. Vendor performance tracking and centralized supplier information enhanced relationship management.
It offered comprehensive functionality for transportation accrual, simplifying the settlement of freight bills. It also provided global reporting capabilities, offering insights into various aspects of the business across different locations. It simplified financial processes with features like automated invoicing and payment tracking and offered real-time financial reporting.
Overcoming Complexities – Embarking on the Journey Towards Digital Transformation Headquartered in Bengaluru, India,...
Revolutionizing Manufacturing Operations with DynaTech’s Top-notch Manufacturing Accelerator The client addresses...
Pursuit to Excellence with DynaTech's Unified Solution The client takes a leading role in shaping, influencing, and...
Implementing a Scalable and Unified Solution to Empower Growth The client is a leading global laboratory automation...
Pioneering Innovation with DynaTech Systems The client specializes in designing and curating interiors for various...